随着科技的进步,世界各国对武器装备、机械产品的性能要求越来越高。传统的碳钢、铸铁等材料已远远不能满足高端装备对质轻、高强、电磁屏蔽等性能需求,因此有色金属及合金逐渐取代钢材而成为重要装备的主体材料,在航天飞行器、智能机器人、高精尖电子仪器设备等领域的应用愈发广泛[1-2]。
目前已知的有色金属有铝、镁、钛、铜、铅、锌、镍、锡、锑、汞等,工业领域以铝、镁、钛、铜的应用最为广泛[3]。为提升装备的机械性能,获得复合型多功能材料,有色金属的表面改性处理已成为材料科学研究的热点,常用的表面改性技术有电沉积、激光熔覆等。电沉积技术具有对基体无损伤、无热影响、不改变基体组织等优点[4-6]。在有色金属表面电沉积一层性能与之互补的金属或合金能够有效提高材料的综合性能[7]。
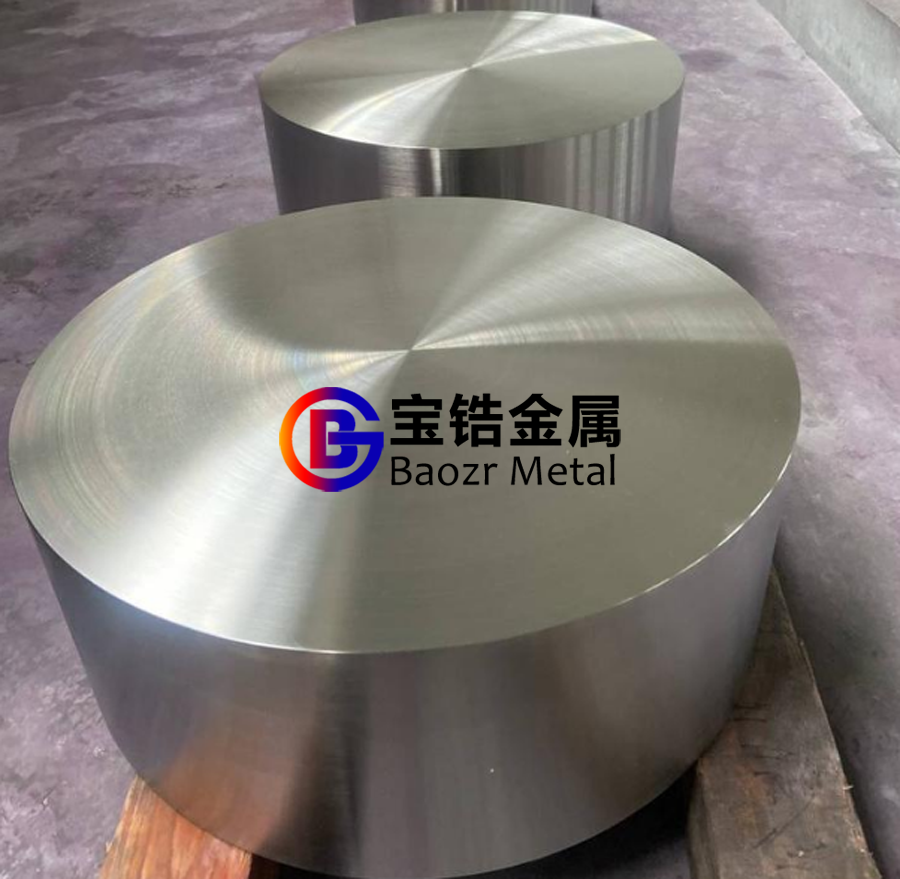
本文针对工业中常用的有色金属铝、镁、钛、铜及其合金的水溶液电沉积和离子液体电沉积表面改性技术的研究进展进行了总结,为进一步研究有色金属表面电沉积提供参考。
1、电沉积技术简介
1.1电沉积技术原理
电沉积技术作为表面工程领域的重要技术,可通过沉积不同的镀层来提高基体材料的耐腐蚀和耐磨损性能,延长零件的使用寿命。电沉积还具有装饰功能,赋予产品平整、光亮的外观。电沉积的主要原理是电解液中的金属离子在外加电源的作用下,通过电化学反应沉积至待镀零件(阴极)表面[8-9]。
1.2离子液体电沉积技术
目前水溶液电沉积已广泛应用于工业生产与科学研究的各个领域,具有技术成熟、基材范围广、成本低、生产效率高等优势。随着科技的进步,离子液体电沉积技术逐步发展起来,并开始应用于有色金属及合金的表面改性处理。相较于传统水溶液电镀,离子液体电镀的研发时间晚,尚未形成工业化规模,但它具有诸多优势,如离子液体中通常不含水,可以避免电沉积过程中发生析氢反应,进而防止镀层发生氢脆现象[10]。离子液体电沉积是采用由有机阳离子与无机或有机阴离子构成的在室温下呈液态的有机盐作为镀液,将待加工零件作为阴极,高纯度目标金属板作为阳极,在外加电源作用下,通过电子运动使目标金属沉积在待镀零件表面形成镀层的过程。离子液体镀液一般具有以下优点:1)沸点低,不易挥发,低蒸汽压,可用于高真空下的反应;2)具有较高的化学稳定性和热稳定性;3)能够溶解无机物和高分子有机物;4)绿色无污染,对环境友好;5)电化学窗口宽,导电性能良好[11]。
1.3镀层种类
通过电沉积可对金属或非金属材料进行表面改性。根据用途,镀层可分为防护性镀层、功能性镀层和装饰性镀层。防护性镀层主要有Zn、Cd及其合金镀层,这类镀层通常要进一步的钝化处理,以提高耐腐蚀性能。功能性镀层主要有硬Cr、Cu、Sn及其合金,可提升基体的表面硬度、导电导热性、可焊性等性能。装饰性镀层主要为Au、Ag、装饰Cr等,能够提升基体的美观性[12]。此外,还可在金属或合金镀液中加入不同类型的第二相不溶性颗粒(如碳纳米管、石墨烯、Al2O3、SiC等),电沉积获得综合性能优良的复合镀层[13]。
2、有色金属表面电沉积技术的研究进展
2.1铝及铝合金
铝在地球上分布广、储量多,比钛、镁、铁的总量还要多,约占地壳的8.2%,其产量在有色金属中居首位。铝及其合金具有密度低、比强度高等优异特性,被广泛应用在航空、航天、国防工业及日常生活中[14]。我国首颗人造卫星“东方红一号”的外壳就是铝合金材质。铝合金在美国弹道导弹的用量为30%~50%,阿波罗Ⅱ号飞船的铝及铝合金用量占75%,空客和波音公司的飞机用铝量高达70%,因此铝被称为“会飞”的金属[15-16]。铝及铝合金的电负性较强,表面极易氧化形成1~3nm厚的氧化铝膜,虽然具有一定的耐蚀性,但由于过薄,在极端条件下反而会加重铝的全面腐蚀。铝的腐蚀多为缝隙腐蚀、点腐蚀、晶间腐蚀、层状腐蚀等形式[17-18]。因此,提高铝及铝合金的耐蚀性、装饰性、功能性和使用寿命具有重要意义。
相比于其他金属表面处理工艺,在铝合金表面电镀可增强铝及铝合金的耐蚀性,有效延长其使用寿命。电镀有着操作温度低的特点,能够使镀层牢固地与金属基体结合。虽然电镀技术有着广泛应用,但是在铝合金电镀前处理过程中,还存在着一些不能忽视的问题和不足,如:工艺复杂,操作工序多;铝合金牌号不同,前处理工艺也不同;产品的合格率很低;前处理溶液使用寿命短;等等。因此要加强铝及铝合金电镀前处理工艺的研究,提高前处理效果。
丁运虎等[19]针对高硅铝合金电沉积前处理过程中存在的磷酸根、氢氟酸、重金属、硝酸、氰化物等物质的污染问题,开发了环保的前处理工艺。他们先采用无磷、低COD(化学需氧量)体系进行除油,接着使用无磷长效碱蚀剂进行碱蚀,然后采用由双氧水、酒石酸、柠檬酸和稳定剂组成的溶液除垢,再用自主研发的无氰、无镍沉锌液和环保退锌液进行沉锌与退锌,所得沉锌层孔隙率低至0.1个/cm2,后续电镀镍层结晶细致,结合力良好。
常德华[20]对铝合金电沉积前处理工艺进行了总结和分析,提出了铝合金镀前清洗喷淋工艺,即在工件浸入清洗水槽的同时开启喷头与超声设备,进而达到高效清洗的目的。他还对浸锌工艺进行了优化,避免加工过程中挂具及其他金属与铝合金发生置换反应,并做好浸锌过程的温度调控,最终使产品的合格率大幅提升。
曾领才等[21]总结了铝合金表面电镀处理的优缺点,对前处理工艺进行了优化改进,提出如下工艺流程:脱脂碱蚀二合一→水洗→酸洗→水洗→去灰→水洗→碱性活化→浸锌(或浸多元合金)→水洗→中性镀镍→水洗→电镀。该工艺适用于多种牌号的铝及铝合金电镀前处理,电镀层分布均匀、结合力良好。
徐金来等[22]开发了一套适用于汽车铝合金轮毂的电镀工艺,具体流程为:除蜡→除油→弱碱蚀→沉锌→预镀镍(铜)→镀高硫镍→镀光亮镍→镍封→镀铬。杜中德等[23]通过脉冲电沉积Ni–W合金对泡沫铝进行表面改性处理,准静态压缩测试结果表明,镀Ni–W合金泡沫铝的峰值应力比未镀和镀Ni泡沫铝分别高了45%和10%,耐蚀性也最优。
哈尔滨工业大学的张建清[24]针对铝合金电镀传统浸锌前处理存在的工序复杂和环保问题(如使用剧毒的氰化物),采用1−丁基−3−甲基咪唑三氟甲烷磺酸盐或1−乙基−3−甲基咪唑三氟甲烷磺酸盐离子液体与乙醇组成的混合溶剂体系,直接在铝合金表面恒流电沉积Cu–Zn合金。所得Cu–Zn合金镀层致密平整,结合力良好,耐蚀性优于浸锌层。该工艺符合绿色环保的要求,有望替代有毒的氰化物浸锌前处理工艺。
电沉积是目前解决铝及铝合金易腐蚀、耐磨性差等问题的主要手段。而铝合金表面电沉积的主要问题在于增强基体与镀层的结合力,因此前处理是铝合金电镀研究的重点之一,应引起重视。
2.2镁及镁合金
镁是银白色的超轻有色金属,密度为1.74g/m3,在地壳中的占比约为1.93%。将Zn、Si、Al等元素添加在镁中即可形成镁基合金[25]。镁合金的比强度高于铝合金和普通钢材,具有良好的切削加工性、热传导性、空间稳定性、电磁屏蔽性、阻尼性等性能,早期较多用于航空航天领域,近年来在汽车、光学仪器、电子、通信、军工等方面的应用增多。但镁及镁合金的化学性质非常活泼,在酸性溶液和中性盐溶液中都容易发生腐蚀[26-27]。因此,在镁合金表面电沉积防护镀层,能够在不改变其轻量化优点的前提下,提升其耐腐蚀性能,延长使用寿命,对于拓宽镁合金的应用具有重要意义。
镁合金活泼的化学性质使其很难直接进行电镀或化学镀,因此适当的前处理工艺极其重要。邢倩[28]在AZ91D镁合金电镀铜前分别进行化学镀镍和浸锌,并优化了这两种前处理方法的工艺流程和参数。
然而无论采用哪种前处理工艺,酸洗活化都极其重要。采用浸锌法时,较佳的酸洗活化工艺条件为:
C2H2O4·2H2O(草酸)12g/L,NaF50g/L,温度25~35°C,时间1~5min。变温浸锌优于恒温浸锌,较优的浸锌工艺条件为:ZnSO4·7H2O30g/L,Na2P2O7120g/L,NaF3g/L,Na2CO35g/L,温度从30°C升至40°C,pH10.2~10.4,10~15min。采用化学镀镍法时,尤其要控制好活化过程的析氢反应,较佳的工艺流程为:电解抛光→热水洗→冷水洗→电解除油→热水洗→冷水洗→酸洗(硫酸24mL/L,硝酸78mL/L,室温,时间1~2min)→热水洗→冷水洗→活化(HF375mL/L,室温,时间10~20s)→冷水洗→化学镀镍。采用化学镀镍前处理时,后续电镀铜层孔隙率低,结合力良好,表面均匀、光亮。
房文静[29]对比分析了AZ91D镁合金表面脉冲电沉积镍和直流电沉积镍的性能,发现采用两种工艺均可在AZ91D镁合金表面获得均匀的Ni镀层,并且结合力都合格,但直流电镀镍层的耐蚀性更好,电流效率更高。
贺严东[30]以1−丁基−4−甲基咪唑氯盐和AlC13制备的离子液体(BMIC-AlCl3)作为电解液,研究并优化了镁合金浸锌及其在离子液体电沉积Al的工艺。结果表明,所得Al镀层均匀平整,与基体间的结合强度达到10.7MPa,耐蚀性良好。
杨海燕等[31]用酸性AlCl3−EMImCl(1–甲基−3−乙基咪唑盐酸盐)离子液体在AZ91D镁合金表面进行电镀铝,研究了不同机械打磨方式及镀液中水含量对Al镀层性能的影响。结果表明,AZ91D镁合金经细砂(粒度W14)以画圆方式打磨及清洗后,可在干燥的AlCl3−EMImCl离子液体中电镀得到均匀致密、结合力强和耐蚀性良好的Al镀层。
常庆明等[32]通过正交试验得到镁合金镀前的较佳酸洗工艺:250g/LCrO3+20mL/L浓硝酸,室温,时间30s。在该较优条件下酸洗后,再用200mL/LH3PO4+100g/LNH4HF2溶液在室温下活化60s,接着用以ZnSO4·7H2O和K4P2O7·3H2O为主成分的焦磷酸盐浸锌液浸渍150s,显著提高了后续电镀镍层的结合力及耐蚀性。
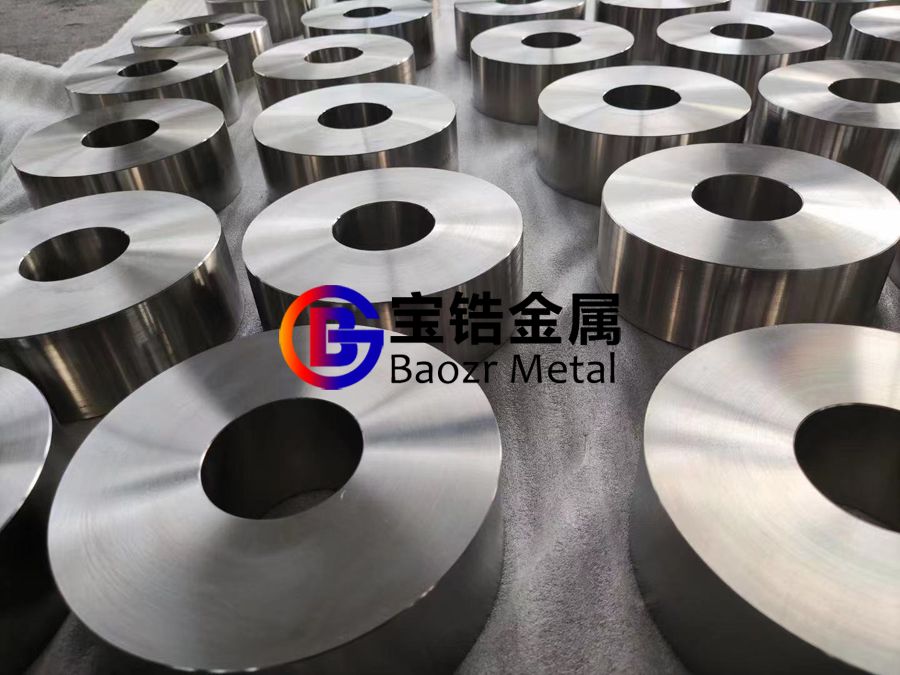
镁及镁合金表面极易形成惰性氧化膜,影响后续电镀的顺利进行及镀层结合力,因此在电镀前应去除表面氧化膜。目前镁合金较常用的电镀前处理方法为浸锌和化学镀镍。浸锌过程需精确控制,直接影响镀层品质。化学镀镍面临的主要问题是镀液呈酸性,会腐蚀镁合金基体。因此,目前镁合金电沉积的工业化应用范围依然有限,虽然有不少新型前处理技术被开发,但多数还停留在实验室阶段,缺少工程化应用验证,故急需开发一种非酸性、适应性强、使用寿命长、无污染的前处理工艺。
2.3钛及钛合金
钛合金被称为“太空金属”,具有密度小,耐蚀性和耐热性好、比强度高,以及生物相容性好等优点,是航空航天、汽车制造等领域不可或缺的有色金属材料[33]。但钛及钛合金的硬度较低,耐磨性差,在加工过程中易粘着,极大地限制了其应用。对钛合金表面电沉积适宜的镀层能够提高其硬度、耐磨性等性能,是解决钛合金在特殊工况环境中存在缺陷问题的有效途径之一[33-34]。
钛合金在许多介质中都容易发生自钝化,不利于获得结合力良好的镀层。针对此问题,于海等[35]先对钛合金表面进行活化和氢化处理,再电镀铜,具体工艺流程为:喷砂→活化(盐酸45mL/L,氢氟酸27mL/L,室温,时间30~45s)→氢化处理(硫酸500g/L,盐酸210g/L,室温,时间30~60min)→电镀铜→钝化→热处理。所得Cu镀层的结合力、焊接性、导电性及耐蚀性均良好。该工艺已成功应用在国内某先进型号战机零部件上。
付强[36]先在TC4钛合金油套管表面预镀Ni中间层,280°C热处理后再冲击镀Ni,最后电镀Cu–Sn合金(配方为:氰化亚铜30~40g/L,锡酸钠35~45g/L,游离氰化钠18~25g/L,氢氧化钠6~10g/L)。所得Cu–Sn合金镀层具有优异的结合力、抗粘扣性和耐蚀性。该研究有助于钛合金油套管产品在油气田复杂腐蚀环境中的推广应用。
袁永超等[37]对比了TC4钛合金镀前活化、活化+化学预镀镍和阳极氧化对电镀Ni–P合金镀层显微硬度、结合力、表面粗糙度和微观形貌的影响。结果表明,前处理工艺对镀层性能的影响较大,较佳的前处理工艺为“活化+预镀Ni”。其中活化工艺条件为:NaBF440g/L,NaNO360g/L,温度80°C,时间10min;预镀Ni工艺条件为:NiSO4·6H2O50g/L,CH3COONa13g/L,NaH2PO2·H2O25g/L,NH4Cl10g/L,pH5,时间5min。所制备的Ni–P合金镀层均匀、平整而致密,结合力好,显微硬度为625HV,表面粗糙度Ra为0.626μm。
赵立才等[38]采用类似工艺对TC2钛合金进行前处理,再电沉积乳白铬中间层,真空退火处理后浸于硬铬镀液中预热2~5min,接着在30~40A/dm2下活化20~60s,最后电沉积硬铬层。结果表明,所得的双层镀铬层与钛合金基体之间结合良好,显微硬度达750HV,耐磨性优良。钛及钛合金电镀的主要难点在于基体与镀层之间的结合力较差。因为钛属于热力学不稳定金属,表面极易形成一层稳定的钝化膜。钛合金表面防护处理的常规方法有转化膜法、金属底层法、避免氧介质法等,但在实际工程应用中这些方法多少都面临工艺繁琐、生产成本高等问题,因此开发钛及钛合金电沉积新工艺具有重要意义。
2.4铜及铜合金
铜及铜合金具有良好的导电、导热等性能,被广泛应用于武器装备、航空航天、舰船制造等领域[39]。但铜及铜合金的硬度低,耐磨性差,不能直接用于磨损冲击环境,而且在一些高腐蚀环境中的耐蚀性也明显不足[40]。因此对铜及铜合金进行表面强化,提高其综合性能,成为了目前的研究热点。
刘建等[41]采用亚硫酸盐体系在黄铜和紫铜表面电沉积Au–Cu−Ni合金,所得Au−Cu−Ni合金镀层光亮、致密,耐蚀性和耐磨性良好,显微硬度为297HV0.025,电阻率为1.84µΩ·cm,接触电阻变化较稳定,能够满足滑动电连接器高导电、高耐磨的要求。
马久明等[42]采用氨基磺酸盐体系在铜基板表面电沉积Ni–rGO(还原氧化石墨烯)复合镀层,与纯Ni镀层相比。Ni–rGo复合镀层的Ni晶粒更细小,石墨烯片均匀分布于镍晶粒之间,有少量镍晶粒被石墨烯片包裹填充至镀层孔洞处。在广东地区的近海域海水中浸泡60d后,Ni–rGO复合镀层表面保持平整,无明显的孔洞,说明该复合镀层能够有效阻挡海水对铜基体的腐蚀。
为提高铜接地材料在弱酸性(酸性)土壤介质中的耐蚀性,方晨旭[43]采用脉冲电镀和化学镀两种方法在铜表面制备了几种镍基合金(如Ni−P、Ni−W−P和Ni−Sn−P)镀层,通过电化学阻抗谱、动电位极化曲线测试和模拟地下铜线腐蚀环境试验分析了它们在不同弱酸性环境下的耐腐蚀性能。结果表明,这些镍基合金镀层相对于铜基体而言都属于阳极性镀层,在弱酸性土壤介质中表现出优于铜基体的耐蚀性,可应用于接地铜材的表面改性处理。
王刚[9]在纯铜表面电沉积Ni−Co−Fe合金镀层,镀液组成为:NiSO4·6H2O220g/L,NiCl2·6H2O40g/L,CoSO4·7H2O20g/L,FeSO4·7H2O10g/L,H3BO350g/L,柠檬酸钠40g/L。在研究了不同因素对Ni−Co−Fe合金镀层性能的影响后得到较佳的电沉积工艺条件为:pH4,温度55℃,电流密度4A/dm2。所得镀层致密、晶粒细小,Co、Ni和Fe的质量分数分别为31.5%、49.7%和18.5%,结合力良好,显微硬度达到818.77HV,有望成为代铬镀层。
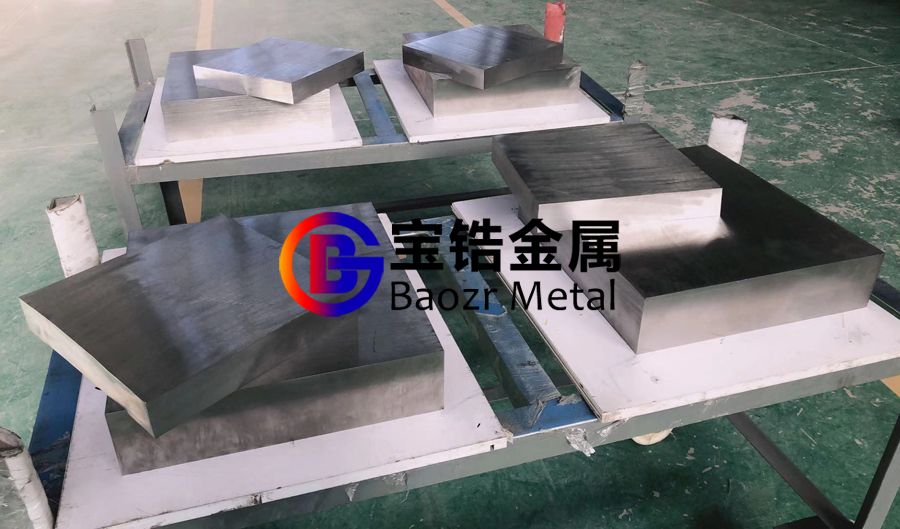
随着人们环保意识的逐渐提升,离子液体电沉积技术目前正逐渐应用于铜基体的表面改性。
Survilienė等[44]采用含0.36mol/LCrCl3·6H2O的[BMIM]BF4(1−丁基−3−甲基咪唑四氟硼酸盐)离子液体,于密闭充氮环境下在铜表面电沉积得到厚度为1~2µm的非晶态黑Cr镀层,但其耐蚀性和硬度都不如晶态Cr镀层,并存在微裂纹、瘤体等缺陷。李晨[45]采用含0.5mol/LCrCl3·6H2O的[EMIM]HSO4(1−丁基−3−甲基咪唑硫氢酸盐)离子液体在铜片表面电沉积Cr,通过研究不同因素对电沉积速率的影响,得到了较优工艺条件为:温度50℃,电流密度50mA/cm2,时间50min。所得Cr镀层厚度为9.2μm,均匀致密,呈晶态结构,耐蚀性优于[BMIM]BF4体系Cr镀层。
铜及铜合金材料易氧化、腐蚀等缺点严重制约着其在高端装备领域的应用。在铜及铜合金表面电沉积既保留了其优良的导电、导热性能,还提高了其抗氧化、耐腐蚀等性能,具有很好的应用前景。
3、结语
随着科技的发展,高端精密装备对有色金属的需求逐渐增加,多功能金属材料将会成为未来航空航天、电子科技、大型装备的主流材料。利用电沉积技术在有色金属表面制备功能多样、性能可控的金属镀层是材料表面工程领域的研究热点。国内的传统水溶液电沉积技术已较为成熟,但一些新型离子液体电沉积工艺仍存在很多不足。加快推进离子液体电沉积技术的研究及工业化应用,不仅对于减少环境污染,避免氢脆隐患及提升产品可靠性具有积极作用,而且对于提升我国高端制造能力,促进我国由制造大国向制造强国转变具有重要意义。
参考文献:
[1] 肖纪美, 曹楚南.材料腐蚀学原理[M].北京: 化学工业出版社, 2002.
XIAO J M, CAO C N.Principle of Material Corrosion [M].Beijing: Chemical Industry Press, 2002.
[2] 刘二勇, 曾志翔, 赵文杰.海水环境中金属材料腐蚀磨损及耐磨防腐一体化技术的研究进展[J].表面技术, 2017, 46 (11): 149-157.
LIU E Y, ZENG Z X, ZHAO W J.Corrosion wear and integrated anti-wear & anti-corrosion technology metallic materials in seawater [J].Surface Technology, 2017, 46 (11): 149-157.
[3] 李多.紫铜在人工海水中的冲刷腐蚀行为研究[D].哈尔滨: 哈尔滨工程大学, 2013.
LI D.Erosion-corrosion behavior of copper in artificial seawater [D].Harbin: Harbin Engineering University, 2013.
[4] 路晨, 王海人, 屈钧娥, 等.碳材料在金属防腐蚀中的应用研究进展[J].腐蚀科学与防护技术, 2014, 26 (3): 254-258.
LU C, WANG H R, QU J E, et al.Progress on research application of carbon materials for corrosion protection of metallic materials [J].Corrosion Science and Protection Technology, 2014, 26 (3): 254-258.
[5] 王一雍, 孙争光, 金辉, 等.结晶器铜板表面激光熔覆 Ni–Co–Al2O 3 复合涂层的微观组织及性能[J].功能材料, 2015, 46 (20): 20148-20152.
WANG Y Y, SUN Z G, JIN H, et al.Microstructure and property of Ni/Co/Al2O 3 laser cladding layer on the surface of mold copper plate [J].Journal of Functional Materials, 2015, 46 (20): 20148-20152.
[6] 魏晓冬.电沉积制备铝钛合金的研究[D].沈阳: 沈阳大学, 2019.
WEI X D.Study on preparation of Al–Ti alloy by electrodeposition [D].Shenyang: Shenyang University, 2019.
[7] 徐滨士, 谭俊, 陈建敏.表面工程领域科学技术发展[J].中国表面工程, 2011, 24 (2): 1-12.
XU B S, TAN J, CHEN J M.Science and technology development of surface engineering [J].China Surface Engineering, 2011, 24 (2): 1-12.
[8] 屠振密.电镀合金原理与工艺[M].北京: 国防工业出版社, 1993.
TU Z M.Principle and Process of Alloy Electroplating [M].Beijing: National Defense Industry Press, 1993.
[9] 王刚.铜表面电沉积 Ni–Co–Fe 合金层工艺及性能研究[D].淄博: 山东理工大学, 2015.
WANG G.The studies of electrodeposition and properties of Ni–Co–Fe alloys on copper [D].Zibo: Shandong University of Technology, 2015.
[10] 薛东朋, 徐霸津, 陈益明, 等.AlCl 3 -EMIC 离子液体电沉积光亮 Al 和 Al–Mn 镀层[J].化工学报, 2015, 66 (增刊 1): 282-286.
XUE D P, XU B J, CHEN Y M, et al.Electrodeposition of bright Al and Al–Mn coatings from AlCl 3 -EMIC ionic liquid [J].CIESC Journal, 2015, 66 (Suppl.1): 282-286.
[11] 周君, 周淑梅.离子液体中低温制备铝技术研究进展[J].上海化工, 2017, 42 (2): 34-38.
ZHOU J, ZHOU S M.Technical progress of aluminum preparation at low temperature in ionic liquids [J].Shanghai Chemical Industry, 2017, 42 (2):34-38.
[12] ELIAS L, HEGDE A C.Synthesis of Ni–W–graphene oxide composite coating for alkaline hydrogen production [J].Materials Today: Proceedings,2018, 5 (1, Part 3): 3078-3083.
[13] 丁小龙, 胡振峰, 金国, 等.轻质碳材料应用于复合镀的研究现状[J].电镀与涂饰, 2017, 36 (11): 604-608.
DING X L, HU Z F, JIN G, et al.Research status of light-weight carbon materials applied to composite plating [J].Electroplating & Finishing, 2017,36 (11): 604-608.
[14] 田荣璋, 王祝堂.铝合金及其加工手册[M].2 版.长沙: 中南大学出版社, 2000.
TIAN R Z, WANG Z T.Aluminum Alloys and their Processing Manual [M].2nd ed.Changsha: Central South University Press, 2000.
[15] 王孟君, 黄电源, 姜海涛.汽车用铝合金的研究进展[J].金属热处理, 2006, 31 (9): 34-38.
WANG M J, HUANG D Y, JIANG H T.Research progress of aluminium alloys for the automotive industry [J].Heat Treatment of Metals, 2006, 31 (9):34-38.
[16] 毕晨, 刘定富, 曾庆雨.2A12 铝合金化学镀镍前处理工艺研究[J].贵州科学, 2016, 34 (3): 88-92.
BI C, LIU D F, ZENG Q Y.A study on pretreatment process of electroless nickel plating on 2A12 Aluminum alloy [J].Guizhou Science, 2016, 34 (3):88-92.
[17] 朱祖芳.铝合金阳极氧化与表面处理技术[M].北京: 化学工业出版社, 2004.
ZHU Z F.Technology of Anodic Oxidation and Surface Treatment on Aluminum Alloys [M].Beijing: Chemical Industry Press, 2004.
[18] 周鼎华.铝合金表面处理技术新进展[J].热处理技术和装备, 2006, 27 (4): 10-15.
ZHOU D H.Recently progress on surface treatment technology of aluminum alloys [J].Heat Treatment Technology and Equipment, 2006, 27 (4):10-15.
[19] 丁运虎, 黄兴林, 邓华才, 等.高硅铝合金电镀环保前处理技术研究[J].材料保护, 2017, 50 (4): 55-57, 72.
DING Y H, HUANG X L, DENG H C, et al.Environmentally friendly pretreatment technology on high-silicon aluminum alloy before electroplating [J].Materials Protection, 2017, 50 (4): 55-57, 72.
[20] 常德华.铝合金电镀前处理技术探究[J].冶金与材料, 2022, 42 (1): 67-68.
CHANG D H.Study on pretreatment technology for electroplating on aluminum alloy [J].Metallurgy and Materials, 2002, 42 (1): 67-68.
[21] 曾领才, 文伟, 谢辉.铝及铝合金电镀前处理工艺的改进[J].电镀与涂饰, 2012, 31 (3): 15-17.
ZENG L C, WEN W, XIE H.Improvement of pretreatment process of aluminum and its alloys before plating [J].Electroplating & Finishing, 2012,
31 (3): 15-17.
[22] 徐金来, 赵国鹏, 胡耀红, 等.铝轮毂电镀工艺应用[J].电镀与涂饰, 2009, 28 (1): 7-9.
XU J L, ZHAO G P, HU Y H, et al.Application of electroplating process for aluminum wheel hub [J].Electroplating & Finishing, 2009, 28 (1): 7-9.
[23] 杜中德, 刘欢, 沈浩田, 等.泡沫铝表面 Ni–W 共沉积及性能研究[J].表面技术, 2020, 49 (10): 233-238.
DU Z D, LIU H, SHEN H T, et al.Ni–W co-deposition and property of closed cell aluminum foam [J].Surface Technology, 2020, 49 (10): 233-238.
[24] 张建清.铝合金表面离子液体电沉积 Cu–Zn 合金过渡层的研究[D].哈尔滨: 哈尔滨工业大学, 2019.
ZHANG J Q.Study on electrodeposition of Cu–Zn alloy transition layer from ionic liquid on aluminum alloy [D].Harbin: Harbin Institute of Technology, 2019.
[25] 安茂忠.电镀理论与技术[M].哈尔滨: 哈尔滨工业大学出版社, 2004.
AN M Z.Electroplating Theory and Technology [M].Harbin: Harbin Institute of Technology Press, 2004.
[26] 刘贵立.镁合金电子结构与腐蚀特性研究[J].物理学报, 2010, 59 (4): 2708-2713.
LIU G L.Electronic structure and corrosion character of Mg alloys [J].Acta Physica Sinica, 2010, 59 (4): 2708-2713.
[27] NIU L Y, JIANG Z H, LI G Y, et al.A study and application of zinc phosphate coating on AZ91D magnesium alloy [J].Surface and Coating Technology, 2006, 200 (9): 3021-3026.
[28] 邢倩.AZ91D 镁合金电镀前处理工艺的研究[D].大连: 辽宁师范大学, 2011.
XING Q.The study of electroplating pretreatment on AZ91D magnesium alloy [D].Dalian: Liaoning Normal University, 2011.
[29] 房文静.AZ91D 镁合金电镀镍及其耐蚀性能研究[D].湘潭: 湘潭大学, 2017.
FANG W J.Study on corrosion resistance of AZ91D magnesium alloy by electroless nickel plating [D].Xiangtan: Xiangtan University, 2017.
[30] 贺严东.离子液体中镁合金表面电沉积铝工艺研究[D].哈尔滨: 哈尔滨工程大学, 2019.
HE Y D.Study on electrodeposition of Al on magnesium alloy surface in ionic liquid [D].Harbin: Harbin Engineering University, 2019.
[31] 杨海燕, 郭兴伍, 吴国华, 等.AZ91D 镁合金在 A1Cl 3 –EMI m Cl 离子液体中电镀 Al 研究[C] // 2009 年全国电子电镀及表面处理学术交流会论文集.[出版地不详: 出版者不详], 2009: 267-271.
YANG H Y, GUO X W, WU G H, et al.Electroplating of Al onto AZ91D Mg alloy from AlCl 3 –EMI m Cl ionic liquid [C] // Proceedings of National Academic Exchange Conference on Electronic Electroplating and Surface Treatment 2009.[S.l.: s.n.], 2009: 267-271.
[32] 常庆明, 张旭, 付至祥, 等.AZ91D 镁合金电镀前处理工艺研究[J].电镀与涂饰, 2021, 40 (3): 202-207.
CHANG Q M, ZHANG X, FU Z X, et al.Study on pretreatment of AZ91D magnesium alloy before electroplating [J].Electroplating & Finishing,2021, 40 (3): 202-207.
[33] 金和喜, 魏克湘, 李建明, 等.航空用钛合金研究进展[J].中国有色金属学报, 2015, 25 (2): 280-292.
JIN H X, WEI K X, LI J M, et al.Research development of titanium alloy in aerospace industry [J].The Chinese Journal of Nonferrous Metals, 2015,25 (2): 280-292.
[34] 冯秋元, 郭佳林, 李蒙, 等.钛合金电镀铬研究现状及应用[J].材料保护, 2018, 51 (10): 109-113.
FENG Q Y, GUO J L, LI M, et al.Research status and application of electroplating chromium on titanium alloy [J].Materials Protection, 2018, 51 (10):109-113.
[35] 于海, 李云飞, 王志煜, 等.TC2 钛合金电镀铜的应用[J].腐蚀与防护, 2015, 36 (5): 432-434.
YU H, LI Y F, WANG Z Y, et al.Application of plating copper on titanium alloy TC2 [J].Corrosion & Protection, 2015, 36 (5): 432-434.
[36] 付强.TC4 钛合金接箍电镀铜锡合金工艺[J].电镀与涂饰, 2019, 38 (19): 1042-1044.
FU Q.Process for electroplating copper–tin alloy on TC4 titanium alloy couplings [J].Electroplating & Finishing, 2019, 38 (19): 1042-1044.
[37] 袁永超, 赵旭升.预处理工艺对钛合金电镀镍−磷合金的影响[J].电镀与涂饰, 2020, 39 (9): 536-539.
YUAN Y C, ZHAO X S.Effects of different pretreatment processes on electroplating of nickel–phosphorus alloy on titanium alloy [J].Electroplating &Finishing, 2020, 39 (9): 536-539.
[38] 赵立才, 高晶, 沙春鹏.TC2 钛合金表面电镀双层铬工艺[J].电镀与涂饰, 2014, 33 (21): 919-921.
ZHAO L C, GAO J, SHA C P.Process for plating double-layer chromium coating on TC2 titanium alloy [J].Electroplating & Finishing, 2014, 33 (21):919-921.
[39] 刘海云, 冯斌, 徐松, 等.不同镀层对铜接地线在弱酸性介质中耐蚀性的影响[J].电镀与涂饰, 2013, 32 (9): 54-57.
LIU H Y, FENG B, XU S, et al.Influence of different coatings on corrosion resistance of copper ground wire under weakly acidic environment [J].Electroplating & Finishing, 2013, 32 (9): 54-57.
[40] 王瑞.Ni–Cu–P 镀层制备及稀土化合物对其腐蚀性能影响[D].哈尔滨: 哈尔滨工程大学, 2013.
WANG R.The synthesization of Ni–Cu–P coating and the effect of RE on its corrosion property [D].Harbin: Harbin Engineering University, 2013.
[41] 刘建, 陈志全, 王钊.Au–Cu–Ni 合金在铜基材表面的无氰电镀[J].贵金属, 2018, 39 (1): 47-50.
LIU J, CHEN Z Q, WANG Z.Non-cyanide electroplating of gold–copper–nickel alloy on surface of copper base [J].Precious Metals, 2018, 39 (1):47-50.
[42] 马久明, 宋士虎, 冼明锏, 等.铜表面镍−石墨烯的电沉积制备及耐腐蚀性能[J].华南师范大学学报(自然科学版), 2020, 52 (4): 43-49.
MA J M, SONG S H, XIAN M C, et al.Preparation and corrosion resistance of Ni–graphene on copper surface by electrodeposition [J].Journal of South China Normal University (Natural Science Edition), 2019, 52 (4): 43-49.
[43] 方晨旭.铜表面镍基多元合金镀层的制备与耐蚀性研究[D].长沙: 湖南大学, 2015.
FANG C X.The study of preparation and anti-corrosion performance of nickel-base multielement alloy coatings on Cu substrate [D].Changsha:Hunan University, 2015.
[44] SURVILIENĖ S, EUGÉNIO S, VILAR R.Chromium electrodeposition from [BMIm][BF 4 ] ionic liquid [J].Journal of Applied Electrochemistry,2011, 41 (1): 107-114.
[45] 李晨.1-乙基-3-甲基咪唑类离子液体三价铬电沉积铬镀层的研究[D].株洲: 湖南工业大学, 2015.
LI C.Study on electrodeposition of chromium coatings based on Cr(III) bath using 1-ethyl-3-methylimidazole ionic liquid [D].Zhuzhou: Hunan University of Technology, 2015.
相关链接